- Website
- Location
- Company size
- 1-10 people
- Company type
- Private Limited
- Markets
Manufacturing Intelligence careers
We’ve built the world’s first Cloud Native, SaaS, Autoscaling, fully automated, Fault Tolerant, Industry 4.0/IIoT, Physics Enhanced, Real-time Spatiotemporal Digital Twin for Mining. It’s a mouthful and it’s a game changer! It’s a new class of software in mining.
Never before has any mining operation been able to have the rich, accurate, real-time visibility of their operations that the MI software is engineered to provide. Starting from geology models, through blasting (accounting for movement, mixing and particles size distribution), bucket by bucket, truck by truck, dozing, stacking, reclaiming, draining, processing, railing, port and shipping.
This level of accurate and richer visibility of material through the value chain enables far tighter optimisation of blends that not only account for grade optimisation but also plant throughput optimisation, resulting in lower unit costs and higher throughput.
Further, as full spatiotemporal history is collected, combined with never before possible granularity and accuracy of material genealogy, Geologists, Metallurgists, Drill an Blast Engineer and Mine Engineers will benefit from unparalleled estimated to planned to measured data sets enabling easy to identify opportunities to improve models, measures and processes.
The software, by necessity, is cloud native. The data events to be processed are so rich in content and high in volume (many millions of events in a given shift) that there is no way traditional software architecture approaches can deliver the performance required to support the reality of a real-time digital twin for mining.
Furthermore, the MI team has significant expertise in i4.0 interoperability standards and has designed the software to natively support the various i4.0 best practice interfaces for information exchange with other mining software packages.
Never before has any mining operation been able to have the rich, accurate, real-time visibility of their operations that the MI software is engineered to provide. Starting from geology models, through blasting (accounting for movement, mixing and particles size distribution), bucket by bucket, truck by truck, dozing, stacking, reclaiming, draining, processing, railing, port and shipping.
This level of accurate and richer visibility of material through the value chain enables far tighter optimisation of blends that not only account for grade optimisation but also plant throughput optimisation, resulting in lower unit costs and higher throughput.
Further, as full spatiotemporal history is collected, combined with never before possible granularity and accuracy of material genealogy, Geologists, Metallurgists, Drill an Blast Engineer and Mine Engineers will benefit from unparalleled estimated to planned to measured data sets enabling easy to identify opportunities to improve models, measures and processes.
The software, by necessity, is cloud native. The data events to be processed are so rich in content and high in volume (many millions of events in a given shift) that there is no way traditional software architecture approaches can deliver the performance required to support the reality of a real-time digital twin for mining.
Furthermore, the MI team has significant expertise in i4.0 interoperability standards and has designed the software to natively support the various i4.0 best practice interfaces for information exchange with other mining software packages.
Senior Software Engineer
Remote • Australia
$130k – $210k • 0.0% – 1.0%Bill Poole
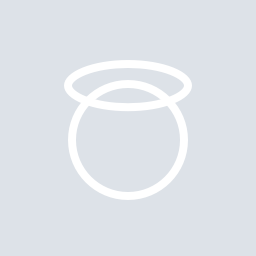
John Kirkman
Worked at Manufacturing Intelligence